SEMANA 7
KAOURO ISHIKAWA
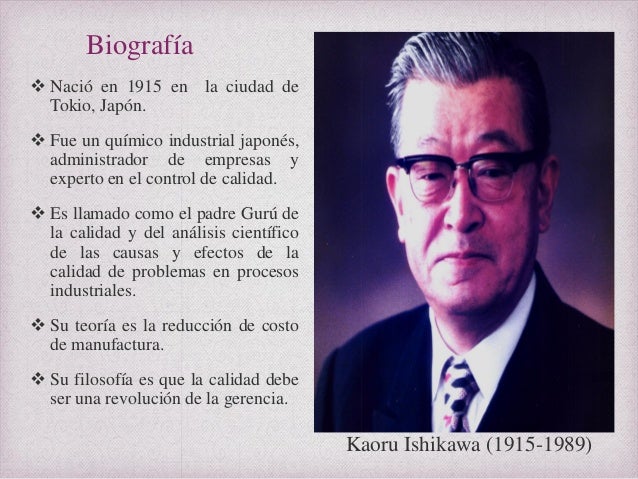
SHIGEO SHINGO
SHIGEO
SHINGO
BIOGRAFIA
BIOGRAFIA
Nació en Saga,
Japón, el 8 de enero de 1909.
ShigeoShingo (1909-1990),
fue un ingeniero industrial japonés que se distinguió por ser uno de los
líderes en prácticas de manufactura en el Sistema de Producción de Toyota. Se
le acredita haber creado y formalizado el Cero Control de Calidad, que resalta
mucho la aplicación de los Poka Yoke, un sistema de inspección en la fuente.
Nació en Saga, Japón, el 8 de enero de 1909. Estudió en
la Escuela Técnica Superior de Ingenieros, en Saga, donde descubrió el trabajo
de Frederick Taylor, fundador del movimiento conocido como "Organización
Científica del Trabajo".
Durante la década de los 40 Shingo
estudió y aplicó el Control Estadístico de la Calidad. En 1961, luego de una
visita en Yamada Electric, Shingo comenzó a introducir instrumentos mecánicos
sencillos en los procesos de ensamblaje, con el objetivo de prevenir que las
partes sean ensambladas erróneamente, entre otras que daban señales de alerta
cuando un operario olvidaba una de las partes.
En 1977, luego de una visita a la
planta de la división de máquinas de lavar de Matsushita en Shizuoco, se
consiguió un mes entero sin defectos en una línea de ensamblaje con 23
operarios. Así, Shingo llegó a la conclusión de que el Control Estadístico de
la Calidad no era necesario para conseguir cero defectos, sino que bastaba la
aplicación de Poka Yoke e inspección en la fuente, siendo esto la base del Cero
Control de Calidad.
Dicho autor quizá sea más conocido por sus contribuciones
al área de la optimización de la producción que a la calidad total; sin
embargo, el argumento cardinal de su filosofía es que una de las principales
barreras para optimizar la producción es la existencia de problemas de calidad.
Su método SMED (cambio rápido de instrumental) funcionará de manera óptima si
se cuenta con un proceso de cero defectos, para lo cual Shingo propone la
creación del sistema poka yoke (a prueba de erroes).
ESTUDIOS REALIZADOS Y SU VIDA PROFESIONAL
Estudió en la Escuela Técnica Superior, en
Saga, donde descubrió el trabajo de Frederick Taylor, fundador del movimiento
conocido como "Organización Científica del Trabajo".
En 1930, se
graduó de Ingeniero Mecánico, en el Colegio Técnico Yamanashi, y comienza a
trabajar en Taipéi Railway Factory. Ahí, observa las operaciones de los
trabajadores y siente la obligación de mejorarlas.
Shingo es el autor de
numerosos libros incluyendo: El estudio del sistema de producción de Toyota,
Una Revolución en la fabricación: El sistema de SMED, Control de calidad cero:
La inspección de la fuente y el sistema Poka-yoke, Estrategias dominantes para
la mejora de la planta, Produccion sin stocks el sistema Shingo para la mejora
continua, y El sistema de gerencia de producción de Shingo: Mejorar funciones
de proceso.
higeo Shingo
es quizá el menos conocido de los gurús de la calidad japonesa en América y
Europa. No obstante, su impacto en la industria japonesa y, recientemente, en
algunas industrias de Estados Unidos ha sido bastante grande.
Distinguido
como uno de los lideres en practicas de manufactura en el Sistema de Producción
de Toyota. Se le acredita haber creado y formalizado el Cero Control de
Calidad, que resalta mucho la aplicación de las Poka Yoke.
APORTES
- El padre de la Administración por Calidad.
- Invento el Sistema Just in Time con Taichi
- El sistema maestro de la empresa Toyota con Ohno.
- Sistema de manufactura esbelta.
- Cambio rápido de instrumento ( SMED)
FILOSOFÍA
Una de las
principales barreras para optimizar la producción es la existencia de problemas
de calidad. Su método SMED (Cambio Rápido de Instrumental) funciona de manera
óptima, si se cuenta con un proceso de Cero Defectos, para lo cual propone la
creación del Sistema Poka – Yoke (a prueba de errores).
El Poka Yoke
- Es una herramienta para orientar el mejoramiento y la prevención de errores en la calidad.
- Este sistema consiste en la creación de elementos que detecten los defectos de producción y lo informen de inmediato para establecer la causa del problema y evitar que vuelva a ocurrir.
El Sistema Poka Yoke esta constituido por:
- Un sistema de detección: cuyo tipo dependerá de la característica a controlar y en función del cual se suelen clasificar, y
- Un sistema de alarma: (visual y sonora comúnmente) que avisa al trabajador de producirse el error para que lo subsane. Asimismo mediante este procedimiento se detiene y corrige el proceso de forma automática para evitar que el error derive en un producto defectuoso.
OTRAS APORTACIONES
- El sistema de producción de Toyota y el justo a tiempo
- Cero inventarios
- El sistema de “jalar” versus “empujar”
IMPORTANTE TOMAR EN CUENTA
Para reducir
defectos dentro de las actividades de producción, el concepto más importante es
reconocer que los mismos se originan en el proceso y que las inspecciones
sólo pueden descubrirlos mas no prevenirlos. El cero defecto no se puede
alcanzar si se olvida este concepto.
Los efectos del
método Poka-Yoke en reducir defectos va a depender del tipo de inspección que
se esté llevando a cabo, ya sea: en el inicio de la línea, autochequeo, o
chequeo sucesivo.
Un sistema Poka-Yoke
posee dos funciones:
- Hacer la inspección al 100%. de las partes producidas
- Si ocurren anormalidades puede dar retroalimentación y acción correctiva
Poka -Yoke está
constituido por:
- Un sistema de detección: cuyo tipo dependerá de la característica a controlar y en función del cual se suelen clasificar, y
- Un sistema de alarma: (visual y sonora comúnmente) que avisa al trabajador de producirse el error para que lo subsane
Aportaciones de Shigeo Shingo
El sistema de producción de Toyota y el Just in time
El sistema de producción Toyota se constituye por sistemas que interactúan entre sí. En conjunto se les conoce como el Sistema Justo a Tiempo, cuya filosofía es "cero inventarios en proceso". No es un solo sistema a instalar, sino una serie de sistemas que se van sumando y permiten llegar a tener una capacidad de producción que garantice la entrega justo a tiempo, es decir, en el momento en que su cliente va a incorporarla a su propio proceso productivo. Según Shingo, perfeccionar este proceso puede requerir varios años.Las ventajas del sistema de “cero inventarios en proceso” son, además, del ahorro financiero:· Los defectos de producción se reducen a cero, ya que al presentarse se detiene la producción, hasta eliminar sus causas.· Al reducir a cero los defectos, los desperdicios de materias primas por productos rechazados se reducen a cero y los consumos en energéticos y otros materiales consumibles se reducen al mínimo.· Las fábricas ocupan menos espacio porque no tienen que guardar inventarios en proceso ni materiales desviados o defectuosos.· El sistema de producción se obliga a trabajar sin defectos, lo que lo hace predecible y, por lo tanto, confiable en cuanto a la entrega justo a tiempo.El sistema de “Pull” vs. “Push”
El concepto de Pull contra Push se refiere a que uno no debe producir una pieza para la línea siguiente, si ésta no la necesita. Las estaciones de trabajo emplean "Kanbans", es decir, tarjetas que indican cuándo la siguiente línea requiere que le envíen materia prima, y cuánta. Para esto también utilizan los "Andons", tableros de luces que mejoran la comunicación a distancia. El sistema Justo a Tiempo constituye un verdadero reto que sólo pueden alcanzar aquellas fábricas que logran resolver todos sus problemas e imprevistos, y dominar y prevenir con bastante exactitud todas las eventualidades de su proceso productivo.Poka-Yoke
Otra parte importante del sistema Justo a Tiempo es el concepto Poka-Yoke, que quiere decir a prueba de error, también conocido como cero defecto. La idea básica es detener el proceso donde ocurra un defecto, definir las causas y prevenir aquellas que son recurrentes. En este proceso no se utiliza el muestreo estadístico. Una parte clave del procedimiento es la inspección de todas las causas de defectos que se presentan durante la producción, para identificar errores antes de que se conviertan en defectos. A diferencia del muestreo estadístico, Shingo utiliza el cien por ciento de inspección. En el proceso productivo, con la ayuda de aparatos especiales, se comprueba, pieza por pieza, que el producto está libre de defectos.Otra parte importante del PokaYoke es el Sistema de Control Visual: los aparatos de control, información, código de colores, distribución de tableros, están estandarizados y crean un lenguaje visual común para distinguir rápidamente lo normal de lo que no lo es. Esto ayuda a llevar la decisión al pie de la máquina. El objetivo es que el operador que actúe como fuente de una falla tenga la información lo más pronto posible, de manera que pueda tomar decisiones y evitar que el error avance en el proceso. Cuanto más pronto y cerca de su origen se pueda prevenir la falla, costará menos resolverla.Otro concepto de gran importancia es su definición de desperdicio. Para Shingo, el objetivo del control de calidad es evitar el desperdicio, entendiendo éste como cualquier elemento que consume tiempo y recursos, pero que no agrega valor al servicio. El Poka-Yoke debe ayudar a identificar el desperdicio fácil y rápidamente.Cinco S's: orden y limpieza. Dos características importantes del sistema de producción Toyota son el orden y la limpieza. No se puede avanzar en la eliminación del desperdicio, si el lugar de trabajo no está debidamente limpio y ordenado. Es posible organizar la estación de trabajo recurriendo a la técnica japonesa de las cinco S's:1. Seri: selección - Distinguir lo que es necesario de lo que no lo es.2. Seiton: orden - Un lugar para cada cosa, y cada cosa en su lugar. Hay que establecer indicadores de dónde va cada artículo, y cuántos de ellos van ahí.3. Seiso: limpieza - Establecer métodos para mantener limpio el lugar de trabajo.4. Seiketsu: estandarización - Establecer estándares y métodos que sean fáciles de seguir .5. Shitsuke: mantenimiento - Establecer mecanismos para hacerlo un hábito.Niveles de prevención Poka-Yoke: Los sistemas de prevención Poka-Yoke pueden ponerse en práctica con sistemas de control en diferentes niveles, cada uno más poderoso que el anterior.Nivel cero. En este nivel se da información mínima a los trabajadores sobre las operaciones estándar. Sólo se les notifica cuándo su trabajo es insatisfactorio, pero en pocas ocasiones saben cuándo y cómo sus esfuerzos contribuyen al éxito o fracaso de la organización.Nivel 1. (Información de resultados de actividades de control): Se informa de los resultados de actividades de control para que cada trabajador, no necesariamente el de nivel superior, pueda ver claramente cómo su desempeño cumple las expectativas. Por ejemplo, los resultados de calidad se exponen en el área de trabajo.Nivel 2. (Información de estándares): Se publican los estándares y métodos para que cada trabajador empiece a identificar las no conformancias en cuanto ocurren, y ayude a corregirlas. Por ejemplo, se exponen instrucciones, procedimientos, muestras de defectos o diagramas cerca de los procesos donde deben aplicarse, como los instructivos de armado de los juguetes.Nivel 3. (Construir estándares directamente dentro del lugar de trabajo): Hacer un estándar de su propio ambiente de trabajo, con sus materiales, equipo o espacio. Explicar cuál es la manera correcta de hacer las cosas. Construir métodos y procedimientos estándar dentro de su propio ambiente de trabajo. Por ejemplo, colocar objetos en carritos de trabajo de colores que coinciden con las líneas dibujadas en los lugares donde deben ir. Cuando se colocan en un lugar equivocado, los colores no coinciden y todos se percatan de ello, como las diagonales en las esquinas, que nos dicen dónde cruzar la calle, o el dibujo en las grabadoras portátiles que nos indican la posición en que deben ir las pilas.Nivel 4. (Alarmas): Para reducir el tiempo de verificación y la velocidad para reaccionar, se debe instalar una alarma visible que avise a los trabajadores tan pronto ocurra un defecto o anomalía. Usar alarmas que avisen que los insumos son insuficientes, o que se necesita ayuda. Por ejemplo, la luz intermitente que aparece cada vez que encendemos el auto y no nos hemos puesto el cinturón de seguridad.Nivel 5. (Prevención): El sistema de control visual nos da el tiempo y la perspicacia para detectar y eliminar anomalías. A través del proceso de verificación, se descubren las causas de las anomalías y se desarrollan maneras para impedir su recurrencia. Por ejemplo, las tapas de los envases de alimento para bebés que se tiran si el frasco ha sido abierto.Nivel 6. (A prueba de errores): El uso de una variedad de dispositivos para verificar el cien por cien de los productos, de manera que estén diseñados a prueba de errores o fallas, y se garantice que la anomalía no se presente de nuevo en el proceso. Por ejemplo, el coche no arranca si la palanca de cambios no se encuentra en la posición de estacionar.
Comentarios
Publicar un comentario